Benefits at a glance:
- Specialist company according to §62, §63 WHG
- Long service life due to acid-resistant stainless steel casing
- Consumption-optimized processes due to cascade operation

Degreasing
Before the thermal treatment in the furnace, the strips need be cleaned from rolling oil and emulsion from the previous rolling process. This degreasing process is of major importance for the quality of the annealed strip, because even low oil or emulsion residues on the strip surface can cause unwanted surface discolorations and, thus, loss in quality.
Modular equipment design
Due to the modular system of the various equipment components, OTTO JUNKER can tailor the degreasing and pickling process to match the customer-specific strip production:
- High pressure spraying chambers
- Squeegee rolls with different rubber and vleece coatings
- Degreasing/brushing machines of „light“ design
- Brushing machines of „heavy“ design, with bearings at both ends
- Spraying chambers for cold and hot rinsing
- High pressure strip edge blow-off
- Strip joint blow-out
- Hot air drier
- Consumption-optimized processes by means of cascade operation
- Stainless steel casing
- Specialized company according to §62 §63 WHG
Pickling and Passivation
After the annealing process, the strip is pickled in order to remove oxide layers on the surface, if any. Depending on the customer’s request, OTTO JUNKER can offer both flood and spray picklers which can be individually adjusted. The finish brushing machines arranged downstream in conjunction with the brush linings selected to match the respective product generate the customer-specific surface pattern. In order to keep the bright strip from oxidating too quickly, the strip is passivated and dried in a spraying chamber before it is coiled again.
Brushing Machines for Degreasing and finish Treatment
OTTO JUNKER develops, designs and builds all the components for copper strip lines at its own premises. Due to their modular arrangement, the individual assemblies can be put together according to the customer’s specific production requirements. For example, there are special brushing machines for degreasing of heavy design for strip finish. These finish brushing machines are equipped with a quick brush change system as well as an automatic brush contact pressure control system which compensates for brush wear. A major advantage is that an oscillation-free brushing operation can be achieved without heavy balancing weights.
Strip Joining Devices
OTTO JUNKER supplies the best strip joining option for all kinds of strip.
Strip stitcher
- For strip thicknesses of up to 4 mm
- For high strip tensions
- Additional wire connection - double safety
- Easy operation
- Low maintenance
Eyeletting joiner
- Particularly for thin strips
- For strip thicknesses between 0.05 and 1.2 mm
- Easy on the rolls
- Low media drag-out
- Very simple and short connection process
Coilers
For a continuous production process with high throughputs, coil handling is of major importance. For this purpose, OTTO JUNKER supplies its own coiler assemblies which allow very short coil changing times:
- Feeding by means of coil lifting cars
- Coiler mandrels for sleeves and/or with clamping slot
- Fully automatic sleeve feeding
- Automatic coiling with belt wrapper
- Paper winder
- Swinging coilers for flying coil change
- Strip accumulators with cable pulls
- Shears
- Strip joint detection
Automation technology
Reliability and ease of operation are essential for high product quality at maximum throughputs. OTTO JUNKER systems benefit from decades of commissioning experience, which is taken into account in the software, hardware and automation technology of each new system.
- Schematic images in visualization provide information about the production process and the function of system components at any time.
- Continuous recording of process data for quality monitoring.
- Integration into higher-level IT systems (Level 3).
strip thickness - strip stitcher | up to 4 mm |
strip thickness - eyeletting joiner | 0.05 mm up to approx. 1.2 mm |
Downloads
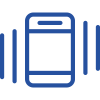
Phone +49 2473 601-0
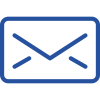
E-Mail sales@otto-junker.com