Cartridge furnaces have proved especially adept in the preheating and homogenizing of rolling ingots of aluminum alloys - particulary for small lot sizes and different dimensions and alloys.
Usually, several furnaces are arranged next to each other which are operated independent of each other. That way, these furnaces offer high flexibility: Each individual batch can be treated differently, e.g. with different temperatures and soaking times. Apart from that, the handling equipment can be shared for serving several furnaces.
The furnaces can be gas-fired or electrically heated. With OTTO JUNKER’s high convection technology, cartridge furnaces are particularly energy efficient.
We supply the entire system, including the charging machine, tilting devices and the feeding and discharge roller tracks, everything from a single source.
Benefits at a glance:
- High flexibility with regard to different alloys and ingot dimensions
- High convection technology for rapid heating and cooling
- Short cycle times with low energy consumption
- Gas-fired or electrically heated
- Annealing under air, nitrogen or protective gas
- Model-controlled furnace controls

Heating system
The furnaces can be either gas-fired or electrically heated. Gas-fired furnaces use self-recuperative high velocity burners with maximum efficiency, while electrical heating allows CO2-free operation.
Using the intense furnace air recirculation, high convection achieves a high heating rate and a homogeneous temperature distribution within the ingot without local overheating and a streak-free surface.
Temperature control is based upon a mathematical model and the actual temperature and achieves a highly homogeneous temperature distribution. Press-on thermocouples monitor the heating up process of the ingots.
Atmosphere
As a standard, the ingots are heated up under air atmosphere. For special applications or alloys, the furnace can also be designed for the use of a nitrogen atmosphere.
Cooling
Cooling of the ingots to rolling temperature after homogenizing inside the furnace takes place in a high-performance cooling system.
The HiPreQ® quench arranged downstream improves the strength of special 6xxx alloys.
Process model
The integrated process model - the “digital twin” - optimizes the entire plant. Due to real-time calculation of the temperature distribution in the ingot, heat input takes place in a precisely controlled manner. That way, the temperature overshoot can be used in the best way possible. It reduces the heating-up time and allows short cycle times, while, at the same time, increasing process repeatability. Press-on thermocouples continuously deliver actual temperature values the process model can be compared with.
By making efficient use of the energy, it reduces costs and saves valuable resources.
Handling
Charging and discharging
The cartridge furnaces are charged and discharged by means of a charging machine. Since several furnaces are arranged next to each other, the handling equipment can be used for several furnaces.
Options
We also offer tailor-made process models for existing furnace plants. We supply the necessary hardware and software and integrate the model into the existing control software.
Scope of supply
We supply the entire plant including charging machine, tilting devices as well as the feeding and discharge roller tracks from a single source. Arrangement and concept are tailored to meet the customer’s individual requirements with regard to space and layout as well as the hand-over and take-over points.
Ingot Length | 5,000 to 7,000 mm |
Ingot width | 1,000 to 2,800 mm |
Ingot thickness | 400 to 800 mm |
Ingot weight | max. 32 t |
Batch weight per Furnace | 100 to 200 t |
Downloads
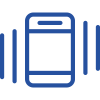
Phone +49 2473 601-0
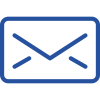
E-Mail sales@otto-junker.com