OTTO JUNKER stands as the foremost supplier of continuously annealing roller hearth furnace systems dedicated to the heat treatment of copper and copper alloys within a protective gas atmosphere. A clientele comprising globally recognized and reputable manufacturers attests to OTTO JUNKER's prominence in the field. The roller hearth furnaces from OTTO JUNKER operate on the proven principle of high convection, ensuring reliable and efficient heat treatment processes for copper and its alloys.
Benefits at a glance:
- No high over-temperature is required (only a few Kelvin above the product temperature)
- No risk of overheating
- Uniform material heating
- Identical mechanical and physical properties
- inner pipe cleaning (CTP)

OTTO JUNKER offers two different roller hearth furnace concepts:
- Jet-Heating
- Mass-Flow
The Jet Heating furnace variant is characterized by an extremely high air velocity, resulting in even higher heat transfer. It is particularly suitable for the heat treatment of thin or single-layered annealed material. This concept does not require high over-temperatures to achieve good heat transfer. The uniform furnace chamber temperature ensures high temperature uniformity in the annealed material.
Mass-Flow furnaces operate with "gentle" high convection and are specifically designed for multi-layered products (LWC-Coils or material that needs to be annealed in bundles). The stack furnace is a proven and space-saving setup where multiple batches are stacked on top of each other for annealing. The Mass-Flow furnace, in addition to its high circulation rate and associated high heat transfer, is characterized by defined flow control and uniform furnace chamber temperature, just a few Kelvin above the material temperature. The stack furnace also stands out for its short length and easy accessibility.
Execution Variants:
- Direct or indirect heating
- Batch or continuous operation
- Open or protective gas atmosphere (typically N2 or up to 100% H2)
- With or without a vacuum chamber
- Gas or electrically heated
CTP (Copper Tube Purging System)
Most Mass-Flow furnaces from OTTO JUNKER are equipped with the Copper Tube Purging System (CTP). The tube inner purging system ensures clean, high-quality copper tubes by flushing out oil vapors generated during heating in the furnace. This significantly reduces carbon deposits on the inner surfaces of the tubes.
Studies show that carbon and oil residue deposits on the inner surface of copper tubes are generally substantially reduced when using the tube inner purging system from OTTO JUNKER compared to systems without protective gas purging. This allows even the most stringent requirements for copper tubes, such as those used in air conditioning units, to be met.
Transport Systems offer the following advantages:
- Available for both furnace variants
- Fewer manual interventions, reducing the risk of bundle damage
- Full integration into existing systems is possible
- Full integration into process technology is also possible
- Automation can be introduced gradually
- Complete elimination of personnel—from bundle production to packaging—as a realistic concept.
throughput | 1,000 kg/h - 10,000 kg/h |
coil diameter | up to 1,400 mm |
coil hight (LWC | up to 700 mm |
straight lengths | up to 6 m |
Downloads
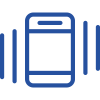
Phone +49 2473 601-0
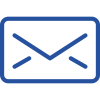
E-Mail sales@otto-junker.com