Benefits at a glance:
- Contactless and virtually draft-free annealing
- Furnaces with protective gas atmosphere and hydrogen operation
- Excellent temperature uniformity across the entire bandwidth
- Reproducible production results
- Continuous operation
- Furnace bypass for exclusive degreasing and pickling operation

OTTO JUNKER is capable of offering complete systems from a single source. This means not only the core component of the system, namely the furnace, is developed and manufactured by OTTO JUNKER, but also the associated components such as:
- Coilers with coil cars, belt wrappers, and automatic sleeve loading
- Shears
- Strip joining systems
- Cleaning and degreasing stages
- Brushing machines for cleaning and surface treatment
- Flood or spray pickling
- Passivation chambers
- Strip storage towers
- Belt-type annealing furnaces up to 850 °C, gas or electrically heated
- Protective gas operation "HN lean" and "HN rich" with up to 50% hydrogen
This ensures that the customer receives precisely the system tailored to their individual product range. Through in-house development and construction, it is guaranteed that the individual components of the system harmonize precisely with each other, benefiting the product quality.
Continuous advancements and innovations, often developed in collaboration with customers, ensure that OTTO JUNKER systems are at the forefront of technology.
In partnership with RWTH Aachen University, with which various institutes closely cooperate in research and development, and through OTTO JUNKER's own development department, machines and systems are continuously improved and optimized. Innovations and close customer engagement are the key factors contributing to our technological advantage
Automation Technology
Reliability and ease of operation are essential for high product quality at maximum throughputs. OTTO JUNKER systems benefit from decades of commissioning experience, which is taken into account in the software, hardware, and automation technology of each new system.
- Schematic images in visualization provide information about the production process and the function of system components at any time.
- Continuous recording of process data for quality monitoring.
- Integration into higher-level IT systems (Level 3)
strip thickness | 0.043 mm - 2.5 mm |
strip width | 300 - 1,300 mm |
strip speeds | up to 120 m/min for max. throughputs |
temperature | up to 850°C |
Downloads
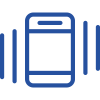
Phone +49 2473 601-0
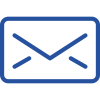
E-Mail sales@otto-junker.com