INDUGA is a subsidiary of OTTO JUNKER GmbH and specializes in Channel melting furnaces, holding and casting furnaces for copper alloys and aluminum, automatic tilting casting device PUMA pouring machine, steel strip coating furnaces, Plasma heating for ladles and casting tundishes.
They offer a range of equipment, including but not limited to:
Form and series casting plant PUMA pouring machine
Channel melting furnaces
Low-pressure casting plants
Vertical continuous casting furnaces
Horizontal continuous casting furnaces
Chip melters
Drum furnaces
Strip coating kettles
Piece coating kettles
Pre-melters
Cathode melters
Plasma technology
Casting furnace Indumat
Low-pressure casting plant in sand casting
Storage furnace for aluminum
Alloy furnaces
Further information on induga.com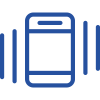
Phone +49 2473 601-0
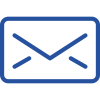
E-Mail sales@otto-junker.com