This type of furnace is specifically designed for solution annealing, quenching and artificial aging of wheels made of cast aluminum.This plant concept places special emphasis on energy savings, ease of maintenance, and flexibility. The wheels are conveyed throughout the entire line using a multi-level lifting-beam system without the need for annealing racks.
Benefits at a glance:
- high temperature uniformity
- easy to maintain
- Compact installation in line or in U-shape
- No wall duct required
- trouble-free material transport
- High level of automation

Heat Treatment System for Cast Wheels
The furnace operates in mixed mode, meaning the wheel diameter can vary between 14" and 24" from wheel to wheel. The furnace is directly heated with natural gas burners in the furnace chamber. Optimal combustion and the use of recuperative burners in the initial zones enable energy consumption optimization. Unlike conventional systems with annealing racks, a rack-free system has been developed to save energy.
Parts to be treated are fed, aligned, measured, and positioned on a roller conveyor. Once the batch is complete, a loading manipulator places it in the furnace. The workpiece transport is carried out by a lifting-beam system, a further development of the step conveyor used in steel heat treatment. A manipulator removes the wheels behind the solution annealing furnace and immerses them in the quenching bath. The parts are then conveyed to the warm storage furnace to complete the treatment. After warm storage, a manipulator takes over the wheels and places them on the discharge roller conveyor. The wheels are cooled in a cold air cooling device after the heat treatment process.
The entire system is controlled by a PLC that monitors all movements, temperatures, and motor operations. A PC with visualization software is used to control all operating parameters and store all operating data.
Heat Treatment System for Cylinder Heads and Engine Blocks
The system includes a loading section (loaded with forklifts), solution annealing furnace, water quenching bath, warm storage furnace, and unloading section.
The air inside the furnace is circulated by high-performance fans, and the furnace atmosphere is directly heated by natural gas burners. In this solution, the exhaust gases from the solution annealing furnace are transported through a single, insulated line to the warm storage furnace. The exhaust is directed to an external combustion chamber (booster) to provide additional heating power if needed for the warm storage furnace (cold start at the beginning of production). The exhaust gases are then distributed to the various zones near the circulation fans.
The energy potential from the exhaust gases of the solution annealing furnace is used to heat the warm storage furnace. Flexibility in the warm storage furnace is achieved by installing modulating burners in the first zone for high heating power when needed. Each furnace has its own transport system, and the two doors can be opened independently to avoid excessive cooling during loading and unloading (chimney effect).
Heat Treatment System for Chassis Components
The system consists of a loading area, solution annealing furnace, water quenching bath with a lift/lower platform and a subsequent drip area, a cross-traveling cart, a straightening area, a warm storage furnace, an air cooling section, and an unloading area. The circulating air is heated directly by natural gas, and the burners are integrated into the flow channel. High-performance fans, located on the furnace ceiling, circulate the air inside the furnace. The components are exposed to the hot furnace atmosphere from all sides, and heating occurs through high convection. The entire furnace is divided into multiple sections that can be controlled separately.
wheel diameter | 14" - 24" |
temperature | 160 - 240°C, max. 300°C |
Downloads
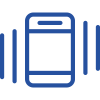
Phone +49 2473 601-0
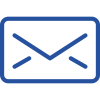
E-Mail sales@otto-junker.com