Application and special features
Pusher-type furnaces are used for preheating and homogenizing of milled rolling ingots of aluminum before hot rolling if the alloys and dimensions of the rolling ingots do not change much. The ingots are run through the furnace one after the other.
With the OTTO JUNKER high conection technology, pusher-type furnaces are optimized for the preheating and homogenizing of rolling ingots before hot rolling from an energy and flow dynamics point of view. They are either gas-fired or electrically heated.
Their main features are very low energy consumption, fully automatic operation and the electronic integration with the hot rolling mill.
If, apart from the standard ingot length, short ingots are also processed frequently, the pusher-type furnace can also be arranged in parallel configuration. That way, the normal length ingots can be preheated in single file and the short ones in double file, so that a higher throughput can be achieved for the short ingots.
In order to reduce energy losses via the doors, we have developed the patented SLE Pusher Furnace.
Benefits at a glance:
- High convection technology for rapid heating and cooling
- Short cycle times and low energy demand
- Gas-fired or electrically heated
- Heating and homogenizing under air, nitrogen or protective gas

Heating system
The furnaces can be either gas-fired or electrically heated. Gas-fired furnaces use self-recuperative high velocity burners with maximum efficiency, while electrical heating allows CO2-free operation.
Using the intense furnace air recirculation, high convection achieves a high heating rate and a homogeneous temperature distribution within the ingot without local overheating and a streak-free surface.
Temperature control is based upon a mathematical model and the actual temperature and achieves a highly homogeneous temperature distribution. Press-on thermocouples monitor the heating up process of the ingots.
Atmosphere
As a standard, the ingots are heated up under air atmosphere. For special applications or alloys, the furnace can also be designed for the use of a nitrogen atmosphere.
Cooling
Cooling of the ingots to rolling temperature after homogenizing inside the furnace takes place in a high-performance cooling system.
The optional HiPreQ® quench arranged downstream improves the strength of special 6xxx alloys.
Process model
The integrated process model - the “digital twin” - optimizes the entire plant. Due to real-time calculation of the temperature distribution in the ingot, heat input takes place in a precisely controlled manner. That way, the temperature overshoot can be used in the best way possible. It reduces the heating-up time and allows short cycle times, while, at the same time, increasing process repeatability. Press-on thermocouples continuously deliver actual temperature values the process model can be compared with. By making efficient use of the energy, it reduces costs and saves valuable resources.
Handling
Loading and unloading
The pusher-type furnaces are loaded and unloaded by means of fork lift trucks. Long-life skid systems with low friction values ensure the safe and smooth transport of the ingots. The skid shoes are conveyed back to the loading end of the furnace either by monorail or by carriage system.
Options
If, apart from the standard ingot length, short ingots are also processed frequently, the pusher-type furnace can also be arranged in parallel configuration. That way, the normal length ingots can be preheated in single file and the short ones in double file, so that a higher throughput can be achieved for the short ingots.
In order to reduce energy losses via the doors, we have developed the patented SLE Pusher Furnace.
We also offer tailor-made process models for existing furnace plants. We supply the necessary hardware and software and integrate the model into the existing control software.
Scope of supply
We supply the entire plant including feeding, pusher and discharge equipment from a single source. Arrangement and concept are tailored to meet the customer’s individual requirements with regard to space and layout as well as the hand-over and take-over points.
Ingot lengths | 3,000 to 8,500 mm |
Ingot width | 800 to 2,300 mm |
Ingot thickness | 250 to 820 mm |
Ingot weight | 32 t |
Batch weight | 200 t - >1,000 t |
Downloads
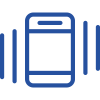
Phone +49 2473 601-0
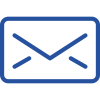
E-Mail sales@otto-junker.com