Our state-of-the-art horizontal heat treatment lines, tailored for aluminum plates or profiles, adhere rigorously to the exacting standards of the aerospace industry, specifically meeting the stringent requirements outlined in AMS 2750 E and AMS 2772 C for the heat treatment of aluminum alloys. These cutting-edge systems are engineered to address contemporary customer expectations, emphasizing high-quality standards in the final products for both the automotive and aerospace sectors, while concurrently prioritizing reduced emissions and energy consumption values.
Benefits at a glance:
- Damage- and scratch-free transport of the panels/profiles
- Uniform metallurgical properties across the length and width of the products
- Even heating on both sides thanks to high convection technology
- Hard and soft quench for even cooling on both sides
- Batch or continuous operation of the oven
- Further expansion stages possible in the future
- Automatic operation

The latest technology from OTTO JUNKER, built upon years of experience, continuous improvement, and innovative research efforts, is tailored to meet customer specifications to their fullest extent.
In addition to prioritizing quality considerations, OTTO JUNKER plate heat treatment lines are meticulously designed for ease of maintenance and operational convenience.
Key components:
Loading and unloading roller tables:
- Dimensioned based on minimum and maximum plate sizes
- Powered conveying rollers ensure proper spacing and synchronism
Furnace section:
- Rapid and uniform heating achieved through optimized flow management and separately adjustable top and bottom heating power.
- Modular structure allows for electrically heated or indirectly gas-fired furnaces with minimal component changes.
- Oscillation during the heating cycle optimizes the length of the heat treatment line.
Quench and aftercooling section:
Stepless adjustments of conveying speed and optimized nozzle spray pattern enable on-the-run plate quenching, reducing equipment length and saving costs.- Integration of hard and soft quench within the same enclosure allows quenching plates of different thicknesses with varying water amounts.
- Cooling rates are customizable, and immersion pumps are designed for easy maintenance.
Dryer:
- Removes water from the water-wetted surface of plates through air wipers and an integrated dryer.
- Dry plates are then conveyed to the exit
Quality Compliance:
- OTTO JUNKER plate ageing furnaces fully comply with customer quality demands, especially regarding temperature uniformity.
- Individually controlled zones and reversible recirculation fans ensure perfect heating across and along the plate.
- Loading options include charging machines or bogies based on requirements and the number of furnaces to be served.
Width | 4,350 mm |
Thickness | 3 - 406 mm |
Lenght | 1.5 - 40 m |
Wall thickness | max. 250 mm |
Downloads
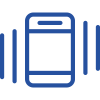
Phone +49 2473 601-0
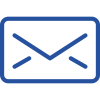
E-Mail sales@otto-junker.com