We supply two different systems for flexible and energy-efficient heating of logs and billets in extrusion shops:
Convection furnaces of unparalleled energy efficiency: These furnaces use special jet heating systems to heat the products. No open flames get in contact with the product surfaces. Therefore, these furnaces are extremely gentle to the logs and billets during heating.
JunkerDynamicHeater® induction furnaces for the highest flexibility: With these furnaces, virtually any temperature profile, the so-called taper, can be set along the log or billet length. Thanks to their high power rating, these furnaces can raise the throughput of isothermal extrusion by more than 20 percent.
Many of our customers report that the combination of both systems – an induction furnace arranged downstream of a convection furnace – has proved as a highly successful solution.
“BILLET pilot”, our advanced mathematical process model, reduces the cycle times and minimizes energy use.
We supply complete furnace lines, including optional equipment such as handling and quenching systems, hot saws and billet washers.
Benefits at a glance:
- High flexibility
- High energy efficiency thanks to the use of an integrated mathematical process model
- HiPreQ® - quenching systems
- Energy-saving

Convection furnaces
The Jet Heating process employed in our convection furnaces is extremely gentle to the material. Heating is exclusively by means of a fluid ((Alternativ: flows of hot air)) ejected at high speed through specially designed nozzle systems onto the billet surface.
While in conventional, gas-fired billet heating systems, the flame temperature is always far higher than the billet temperature, in convection furnaces, the difference between both temperatures can be much smaller. Thus even the tightest temperature tolerances, as e.g. required for certain specialist applications, can be achieved most reliably and with very high repetition accuracy.
The use of high-efficiency burners with integrated heat recovery guarantees energy efficiencies better than achievable with any other concept.
JunkerDynamicHeater®
An important strong point of the induction furnace is its high flexibility: Even in one-off processes, virtually any desired temperature profile along the billet length, also referred to as the taper, can be reliably achieved. This is essential for isothermal extrusions.
The furnace heats up each billet individually. This guarantees very tight temperature tolerances even if billets of different length and temperature are processed.
Besides the induction coil, which is segmented into several zones, the proven OTTO JUNKER IGBT high-performance frequency converter with its wide variation range, plays a key role in achieving the high temperature accuracy of our furnaces. We manufacture these two core components in-house. Other components, such as transformers or water recooling plants, can be supplied as an option.
The digital twin
Process control with the support of our BILLET Pilot system reduces the billet retrieval times. This leads to a reduction in energy costs and shorter cycle times. The mathematical model – the digital twin of the billet – computes the temperature distribution within the billet from the electrical power input of the induction coils. Thus the contact heat can be optimally used, resulting in considerably shorter heat-up times.
HiPreQ(R) quenching systems
To achieve certain metallurgical properties in special aluminium alloys, the billets are subjected to dedicated quenching treatments before they go through the extrusion process. The metallurgical effects of these treatments make it possible to increase the extrusion speed and achieve a superior material quality.
We have developed advanced, high-performance quenching systems that enable the operator to set the cooling rates with high precision and excellent repetition accuracy.
Separate control zones ensure that the specified temperature profiles can be exactly set. The systems come with a teach-in function that generates cooling programs which, in combination with the infinitely adjustable cooling rates, ensure high repeatability of the treatment process. The closed water circuit keeps operating costs down and protects the environment.
Intelligent billet storage
The extrusion logs and billets are stored in vertical, chain- or pallet-type storage facilities.
The storage systems are equipped with a material management system that coordinates, records and archives all material data along the various process stages. The production data of incoming billets are read out from barcodes either automatically or with a manual device. Thus, it is guaranteed that the software uses the correct temperature and length parameters at the furnace, the saw and all other processing stages along the entire production chain. After completion of the heating process, the thermal information is added to the data set of each billet processed, and transmitted to the process control system of the extrusion press together with the respective billet.
Handling equipment
For billet and log handling, we supply standardized components (V-troughs, roller tables, grippers, etc.) individually combined and adapted to the requirements of the respective task. These systems transport the logs and extrusion billets safely, smoothly and quickly from the storage facilities to the extrusion line.
Hot saws
The logs are cut into billets of specific lengths with high-precision hot saws developed by OTTO JUNKER. The optionally available “park cut” system reduces waste to an absolute minimum: If there are, for example, two short residual log ends, the system feeds these short ends both together into the induction furnace for the extrusion press to process them as one single billet. All our saws come with a movable stop and high-precision clamping systems that ensure that the logs are cut exactly to the specified lengths. The metal chips are extracted and compacted in a briquetting press.
Billet and log washer
We supply high-pressure log and billet washers that operate with a closed-loop water system featuring integrated filters for maximum environmental compatibility.
Diameter range of billets | 6 - 24 inch |
Length | 600 - 7,200 mm |
Power rating | 400 - 3,600 kW |
Downloads
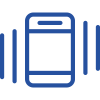
Phone +49 2473 601-0
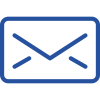
E-Mail sales@otto-junker.com