These channel-type furnaces store molten iron, hold the metal exactly at the specified temperature and heat it to the required pouring temperature.
With their optimally insulated upper vessel and the highly efficient channel inductors, they are the perfect holding furnaces for liquid iron. Their main functions include the decoupling of the casting and melting operations in metal production and the collection and storage of large quantities of molten iron to prepare for the production of large castings or long casting campaigns.
Moreover, these furnaces can help cut energy costs: With time-varying electricity pricing programs, it makes sense to let the melting furnaces produce molten metal in advance during off-peak times and store the excess amount of metal in a holding furnace. Additionally, it is more cost-efficient to continue the metal heating process in a holding furnace using low-priced electricity. In this way, the holding furnace serves as an energy accumulator.
In addition to being energy-efficient and economical, metal holding in the furnace ensures a homogeneous temperature distribution within the metal bath. The closed design of the furnace vessel prevents any undesired gas absorption. As the furnace is inductively heated, there is no metal loss due to combustion.
Benefits at a glance:
- High quality and minimum waste due to precise pouring temperature control.
- Simultaneous filling and pouring.
- Production increase due to optimal utilization of the melting capacities: As soon as a melting furnace has completed a campaign, it can be completely emptied and immediately refilled with the next metal charge.
- Less costs by avoiding residual iron: The melting furnaces can always be completely emptied, and, if any molten iron is temporarily not needed, this can be safely returned to the holding furnace.
- Decoupling of melting and casting.
- At filling weights of 50 t, for example, superheating rates of around 100 °C per hour can be achieved.

OTTO JUNKER channel-type holding furnaces consist of a cylindrical vessel with siphons at the filling and pouring ports. The furnaces are hydraulically tiltable. The inductor – conveniently arranged for easy replacement, if necessary – is flanged to the furnace bottom.
The power supply is infinitely adjustable. An IGBT module keeps the power factor constant at cos phi = 0.99.
We also supply crucible-type holding furnaces for special applications. The advantage of these furnaces is that they can be completely emptied. The crucible-type variant is recommended for alloys susceptible to deposit accumulation because of the risk of channel clogging. However, the efficiency of crucible furnaces is distinctly lower than that of channel-type ones.
+ Low electricity consumption
The upper furnace vessel features a multi-layer ceramic wall. Due to this design, channel-type furnaces consume considerably less energy during operation than crucible furnaces.
+ High throughput
Using a holding furnace in the casting shop makes it possible to empty the melting furnaces as soon as the target temperature and analysis of the heat have been reached. Thus, the next melting campaign can start without delay.
+ An optimal storage unit for continuous melting furnaces
In a channel-type holding furnace, metal tapping and filling can be performed simultaneously. This feature makes it an ideal forehearth of cupola or shaft-type furnaces.
+ Homogeneous temperature distribution within the furnace
The water-cooled U or W inductor channels operate with efficiencies better than 90 percent, while the jet current guarantees a homogeneous temperature distribution within the furnace.
+ Digitalization with JuMI Hold
The Junker Melting Interface – JuMI Hold – optimizes process control and monitors the entire holding and superheating processes. It visualizes all relevant process data, including the furnace content, temperature curves and channel wear, on user-friendly displays.
The system is based on a Safety PLC with WinCC touchscreen visualization. It provides the operator the option to use online support and establish data links to higher-level systems, via an OPC UA interface, for example.
Typical use | Liquid metal holding |
Design | Channel induction furnace |
Furnace type | Tiltable |
Capacity | 25 - 150 t (for iron) |
Electrical power | From 400 kW up to 2,600 kW |
Tapping mode | By tilting, into ladle or tundish |
Downloads
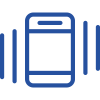
Phone +49 2473 601-0
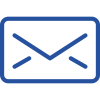
E-Mail sales@otto-junker.com