In automatic sand casting lines, it is essential that the mould filling process is performed with utmost precision to achieve high-quality castings. Pressurized pouring furnaces using high-precision stopper and pouring systems are the solution of choice here.
OTTO JUNKER’s RGD Ge pouring furnace consists of a vessel pressurized with air or inert gas. The vessel features siphons at the filling and pouring ports. End of pouring is controlled by means of a stopper system. A highly efficient channel inductor, flanged to the vessel, holds the molten metal at the desired temperature. The power supply is infinitely adjustable. An IGBT module keeps the power factor constant at cos phi = 0.99. For specific applications and special materials, we also supply the pouring furnace with a crucible-type holding unit.
Benefits at a glance:
- High quality and minimal scrap thanks to constant casting temperature and precisely controlled, slag-free pouring.
- Continuous pouring also during refilling
- Fewer metals returns as a result of the precisely controlled pouring process
- Production increase through optimized used of moulding line capacity
- Cost reduction through avoidance of residual iron
- Decoupling of casting and melting
- Reduction of personnel costs through automated casting

This OTTO JUNKER pouring furnace consists of a cylindrical vessel with an exchangeable flanged-on siphon at the filling and the pouring port. Pouring is controlled by a rod-and-nozzle stopper system. The furnace is pressurized in order to maintain a constant hydrostatic bath level above the pouring nozzle.
The inductor – conveniently arranged for easy replacement, if necessary – is flanged to the furnace bottom or arranged at the side. The filling and pouring ports can be arranged at +/- 90° or 180° from each other.
For emptying, the vessel is hydraulically tiltable through the filling port axis. It is mounted on a length- and crosswise movable carriage. Thus, the pouring spout can be positioned exactly above the sprues of the sand moulds.
Pressurized dried air or inert gas is injected into the vessel, causing the molten metal to rise through the pouring siphon into the pouring spout closed by the stopper system. The bath level in the pouring port is controlled by means of a floater gauge or non-contact laser-based measurements. In case the filling level in the pouring chamber is too high, the pressure in the pressurized chamber is automatically reduced to bring the bath level back to the correct level.
The pouring rate can be infinitely adjusted by varying the lifting height of the stopper rod during pouring.
Our customers can choose between a pneumatic or an electrical linear system to actuate the stopper rod. In the event of a power failure both systems are equally safe as they both close by gravity.
For direct injection of inoculants into the pouring stream, we supply our Optistream inoculation system as an option. The Optistream unit is linked with the JuMI Pour control system.
+ Repeatable casting quality through automatic mould filling
Operators wishing to automate the stopper actuation to achieve repeatable mould filling, can obtain as options our camera-assisted control system, Teach In Cam, or our Belycast camera control system, which also includes a teach-in function.
+ Increased production rates through uninterrupted pouring
Even during furnace refilling, the bath level above the pouring spout is precisely controlled. Thus, it is possible to continue the mould pouring process without interruption.
+ Suitable for spheroidal graphite cast iron
As the filling and pouring ports, as well as the inductor at the furnace bottom, are very easy to clean, the furnace is also suitable for processing spheroidal graphite cast iron. The furnace can also be supplied with a crucible-type inductor as an option.
+ Digitalization with JuMI Pour and Belycast
The JuMI system optimizes process control and reliably monitors the entire casting process, ensuring maximum safety. The system is based on a Safety PLC with WinCC touchscreen visualization. It provides the operator the option to use online support and establish data links to higher-level systems, via an OPC UA interface, for example.
Typical use | Metal casting in automatic sand casting lines |
Design | Channel induction furnace |
Furnace type | Pressurized pouring with stopper rod system |
Capacity | 1.5 - 40 t (for iron) |
Electrical power | From 100 kW up to 1,200 kW |
Tapping mode | Continuously clocked |
Stopper control | Optical, by means of camera or laser with teach-in function |
Downloads
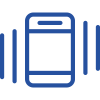
Phone +49 2473 601-0
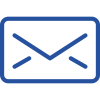
E-Mail sales@otto-junker.com